1. Structural features and working principles
1.1 Overall structure
The basic structure diagram is as follows:
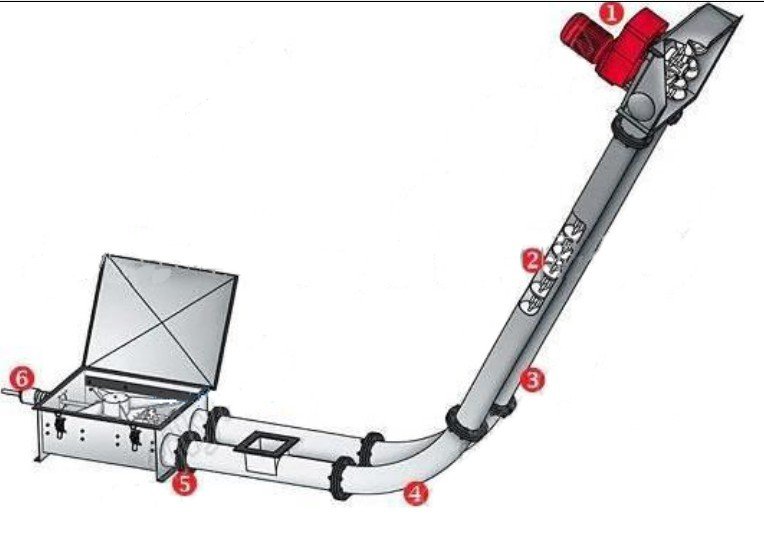
1 Driving part 2 Loading transmission part 3 Straight conveying 4 Turning conveying 5 Butt flange 6 Tensioning device
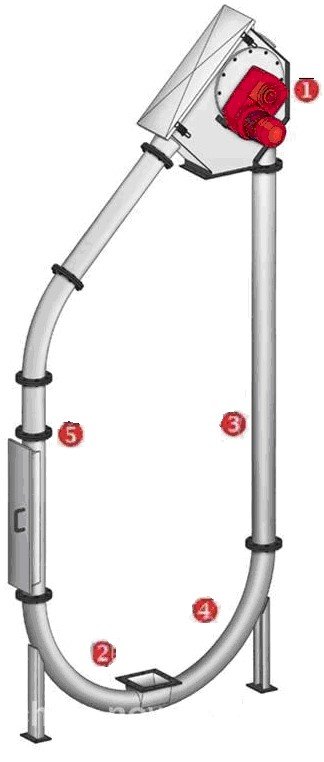
1 Driving part 2 Loading transmission part 3 Straight conveying 4 Turning conveying 5 Butt flange 6 Tensioning device
1.2 Working principle and main components
Before starting to operate the pipe chain conveyor, it is necessary to fully understand the contents of this manual.
Before starting to operate the pipe chain conveyor, it is necessary to fully understand the contents of this manual. If the pipe chain conveying equipment is operated according to the procedures stated in this manual, it will operate safely and soundly. If the equipment is not operated as described in the manual, our company will not be responsible for any consequences that may occur.
The contents of our products and manuals are subject to technical innovations as new developments occur.
Electrical machinery and equipment are used in current industries. If they are not operated according to safety instructions, dangers may easily occur during application. In this regard, it is necessary to prevent unauthorized movement, improper use, incorrect operation or unreasonable maintenance, which may cause personal injury or property damage.
Technical characteristics
(Equipment specifications and performance parameter reference table)
D Pipe diameter | Conveying capacity(m³/h | Sprocket speed (rev/min) | Chain plate linear speed (m/s) | (Conveying 10 meters) Motor power(kw) |
DN80 | 4 | 20 | 0.2-0.4 | 4 |
DN100 | 8 | 18 | 0.2-0.4 | 5.5 |
DN150 | 16 | 15 | 0.2-0.4 | 7.5 |
DN200 | 28 | 12 | 0.2-0.4 | 11 |
DN250 | 48 | 10 | 0.2-0.4 | 15 |
DN300 | 60 | 8 | 0.2-0.4 | 18.5 |
2. Characteristics of pipe chain conveyor
- The structure is compact and the conveying direction can be changed in three dimensions.
- Fully enclosed conveying, no dust spillage, clean and environmentally friendly.
- During the material transportation process, energy consumption is low, which minimizes operating costs.
- The maximum horizontal conveying distance is 60 meters, and the maximum lifting height is 40 meters. The maximum conveying capacity can reach 100 m³/h.
- There is no dead zone in the transportation pipeline.
- The conveying disc can be made of non-metallic material to minimize noise.
- Low maintenance cost.
- Long service life.
- Explosion-proof design and air-tight design are available.
- Ensure the integrity of materials to the greatest extent.
3. Advantages of pipe chain feeding system
- Volumetric conveying device can realize conveying and measuring of materials. It is easy to realize centralized control, improve the degree of automation, and meet the requirements of modern enterprises for environmental protection.
- Compact structure, small space occupation, flexible adjustment, and the conveying direction can be changed three-dimensionally according to the site layout.
- The conveyed materials are in a sealed state from the entrance to the exit, and the materials have no contact with the outside world; the dust-free requirements can also be achieved without a dust collector at the exit. When transporting flammable and explosive materials, protective gas can be filled to ensure safe production and transportation.
- Materials are transported smoothly along the material pipe, basically avoiding relative internal movement between materials, with less material damage, and gentle curves can also ensure material integrity to the greatest extent with the support of technical parameters.
- The optimized sprocket design and clearance fit with the chain minimize the wear between the wheel and chain; at the same time, the hardening treatment of the chain and sprocket greatly improves the wear resistance.
- Select trays of corresponding materials for different materials, which have extremely low friction coefficient and stable conveying performance.
- All pipe chain conveyors we produce use self-developed calculation programs to maintain the necessary static friction and tensioning force on different components such as the conveyor pipes and curved parts, providing high-precision data for designing low noise and low wear.
4. Main purposes and scope of application
The equipment covered by this manual is intended for use in a variety of operations under normal conditions. If used for other purposes or in potentially hazardous environments, special safety regulations must be followed and the equipment must be equipped with equipment suitable for the corresponding purpose.
Fine chemicals: pigments, dyes, coatings, carbon black, titanium dioxide, iron oxide, ceramic powder, heavy calcium, light calcium, bentonite, molecular sieve, kaolin, silica gel powder, activated carbon, etc.
Pesticide ores: urea, ammonium chloride, ammonium bicarbonate, soda ash, solid pesticides, tungsten powder, pesticide additives, copper concentrate powder, coal powder, phosphate rock powder, alumina powder, etc.
Building materials: cement, clay, yellow sand, quartz sand, clay powder, silica, limestone powder, dolomite powder, sawdust powder, glass fiber, silica, talc powder, etc.
Food industry: flour, starch, cereals, milk powder, food additives, etc.
4.1 Use environmental conditions
It is suitable for places where the ambient temperature does not exceed 40℃ and the humidity is 95%. The maximum working temperature of the motor does not exceed 95℃.
4.2 Precautions for safe use
Preparations before startup
- Check whether there is an appropriate amount of lubricating oil in the bearing and whether it is operating normally.
- Check whether all fasteners are loose and retighten if any.
- Check whether there is metal or other unbreakable debris inside the machine.
- Check whether the gap between the housing and the moving parts meets the requirements.
Rotate the equipment and observe whether it is normal, whether the rotation direction is correct, and whether there is friction between the material plate and other parts.
- The machine can be started only after checking that there are no abnormal factors.
- If any abnormality occurs after starting, stop starting immediately. The device must be started again only after checking the cause and eliminating abnormal conditions.
4.3 Maintenance and use
- Feeding can only begin after the equipment is in normal operation.
- Materials must be added evenly and distributed on the working surface of the working part. To prevent sudden load increase on the motor.
- Check the situation regularly and clear it immediately if there is any blockage.
- Under normal working conditions, the maximum temperature of the bearing shall not exceed the specified requirements. If it exceeds the requirements, the machine should stop immediately to find out the cause and eliminate it.
- Feeding should be stopped before parking, and the motor can be turned off only after the materials in the room are completely discharged.
- If the transmission chain is damaged, it should be replaced in time.
- When the product particle size needs to be adjusted, the material plate of appropriate specifications can be replaced.
- When the amount of vibration suddenly increases, stop the vehicle immediately and check and eliminate the cause.
5. Maintenance and repair
Make sure the machine will not restart, close all control boxes and take away the keys! Set up warning signs!
5.1 General requirements
This machine should prevent iron parts and other foreign objects that are not easily broken from entering the machine. Three minutes after the equipment is started, start the feeder to feed the equipment after confirming that it is normal. The equipment must stop feeding and confirm that the material in the machine cavity has been completely removed before it can be shut down.
Pay attention to the sound of the machine and monitor the changes in current and voltage of the instruments in the central control room. If an abnormality is found, stop the machine immediately for inspection. Only after the cause is identified and dealt with can it be restarted.
5.2 Specific instructions for machine maintenance
The prescribed maintenance, monitoring and inspection measures must be carried out regularly by trained personnel to avoid faults interrupting the process. Deviations from normal performance (high energy input, high temperatures or vibrations, unusual noise or odors, reaction forces of monitoring equipment) indicate The equipment has varying degrees of damage. In order to avoid errors that directly or indirectly cause serious damage to property or injury to personnel. Relevant maintenance personnel should be notified promptly.
If you are unsure or have doubts about it, disconnect power from the device immediately.
The maintenance of pipe chain conveyors is basically limited to setting the tightness of the chain. The bearings selected for this system are original products from well-known domestic and foreign manufacturers. They do not require daily maintenance. Under normal conditions, their operating life is more than three years. Only under difficult conditions, it is necessary to inspect them, and inspections must be carried out by experienced personnel. To avoid damage to the system, the following conditions can be considered severe:
- The current temperature exceeds 100 degrees Celsius
- Water enters the bearing
- Unavoidable dust pollution
- The humidity is high and the equipment is used occasionally.
5.3 Check and maintain intervals
In order to ensure that all parts of the machine are in good working condition and avoid failures, a planned pre-repair system should be established.Implementation of the maintenance plan is after work – hours.
Item | Interval Time | Label |
Check chain tension | Shift/time | Monitor all conditions, identify situations and make appropriate changes |
Adjust the chain tension | According to the on-site working conditions | Judge based on the debugging and use of the tensioning joint |
Check chain length and tensioner operation | Every 500 operating hours | |
Shorten the chain | Depending on the working conditions on site | the chain must be shortened by multiples of 2 |
Check the tray for wear | Every 500 operating hours | |
Check bearings and transmission parts | Every 1000 operating hours | |
Check pipe wall thickness | Every 500 operating hours | |
Check sprockets | Every 500 operating hours | |
Check whether there is any hanging material contamination at the entrance | Every shift | |
Check packing seal | Every shift |
5.4 Lubrication
Distribution of lubrication points
Lubrication parts: Bearings of rotating parts such as active boxes, passive boxes, corner boxes, etc.
Selection of grease
It is recommended to use the following grades, see the table below
Manufacturer | Lubricant name | Consistency | Thickener | Operating temperature range |
Red Star Grease | Jiejia Lithium Grease | 2 | Lithium | -20°C/+120°C |
The grease added during bearing operation should be of the same brand as the grease initially used. If you want to change brands, the bearings should be cleaned before filling.
Use high temperature resistant grease in high temperature environments.
Notice:
1、The filling container and oil filling cup should be clean to prevent dust or debris from entering.
2、If the oil cup cannot be filled with grease, the reason should be checked and replaced.
3、It is strictly prohibited to mix different brands of lubricating grease.
6. Analyzing and Troubleshooting Faults
Failure | Possible causes | Actions to be taken |
The chain rolls out of the sprocket | The chain is too loose | Tension the chain. Simple transmission to detect the tensioner |
Foreign material | Remove foreign objects and check whether the material is pure | |
The material tray is worn | Replace the conveyor disc | |
The drive wheel is worn | Replace the sprocket | |
The chain is twisted | Locate the chain connection and untwist the chain | |
The transmission direction is wrong | Replace the motor poles | |
There are residues in the conveyor | Check the materials and install cleaning devices | |
The bearing is worn | Replace the bearing. | |
There is material residue in the pipe | Install a cleaning disk or clean the conveyor. | |
The chain is too tight | Adjust the tension according to the manual | |
The conveyor is not running | Materials remaining in the pipe are crystallized and solidified | Remove the conveyor and clean it |
The conveyor is loaded with too much material | Open the inspection hatch, use a winch to pull out the chain, and then clean it | |
Gearbox defective | Replace | |
The packing is leaking | The packing seal is worn | Tighten the bolts regularly, compress the packing, and add packing sealing filler. |
Wear standard
When is a component considered to have exceeded its maximum wear limit?
Spares | When do parts need to be replaced: |
Conveying discs: | The diameter of the largest disc wear point is ≤ 70% of the original disc diameter |
Sprocket | The contact point wear of sprocket teeth is ≥8mm |
Pipes | When the pipe wall is less than 2 mm, please note: Straight pipes can be rotated up to 7 times, because wear usually occurs at the bottom of the pipe. |
Bearings | When there is noise or overload rotation |
Packing seal | When leakage occurs |